How To Prevent Administrative Error Shrink
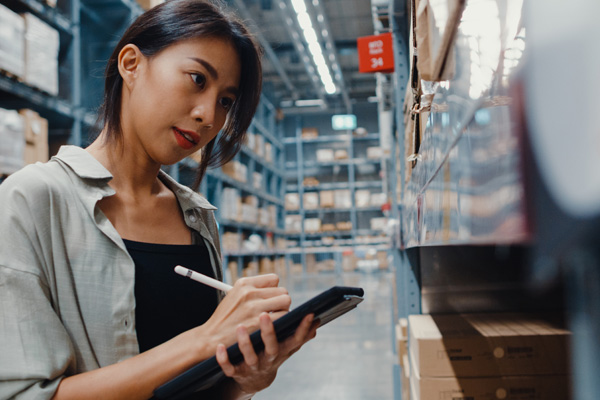
Table of contents:
Not all retail loss comes from theft. In fact, administrative error can cause significant inventory losses for your business. According to the National Retail Federation (NRF), administrative and paperwork errors are responsible for up to 18.8 percent of retail shrink. Unlike shoplifting, organized retail crime (ORC) or employee theft, I see administrative error shrink as completely within the retailer’s control. By following a strict inventory control process and consistently training your employees, you can prevent administrative error from affecting your bottom line.
What Does Administrative Error Shrink Look Like?
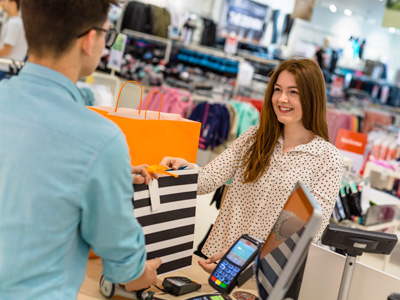
Administrative error shrink is often referred to as “paper shrink” because it comes from information that has been incorrectly recorded — from inventory checks to sales promotions. Here are some common types of administrative errors that I’ve seen:
Inventory errors: Poorly managed inventory control is probably the most widespread type of administrative error shrink. If a retailer isn’t counting their stock correctly, this could lead them to find shortages that might not be real. Once they start investigating these “losses,” the retailer could end up wasting their time, simply because they don’t have an accurate view of their inventory.
Receiving and shipping errors: It’s not uncommon for a vendor to find they’re unable to fulfill your order exactly. For example, if a retailer orders 100 black shirts, a vendor might only be able to give them 75 black shirts and substitute the rest with 25 red shirts. The issue comes when the retailer receives the order and doesn’t check the shipments to ensure they have accurate information about their incoming stock. If they didn’t realize the order wasn’t fulfilled correctly in the beginning, they might later record the missing 25 black shirts as an actual loss, rather than an error with the vendor.
Stocking errors: These errors include merchandise that has been improperly stored or overstocked products that can’t be sold after a certain date. For example, if a grocery store receives a shipment of frozen pizzas but they aren’t immediately stored in a freezer, they could go bad and will have to be discarded before they can even be sold, and then they will not be accounted for properly. Similarly, a retailer that doesn’t have an accurate record of their inventory might unintentionally order more merchandise than they can sell, which is a major issue for perishable items or seasonal products.
Damaged merchandise control: How your organization manages damaged merchandise is critical to the overall outcome of your inventory. Unfortunately, some employees don’t understand the importance of the damages process. Because they know the damaged product will be thrown out anyway, sometimes they will just discard the merchandise without going through the process of reconciling the damages and taking it out of inventory. The simple mistake of not documenting damages can cause inventory loss without any theft.
Reduced standards: I would say every administrative error loss is preventable if a retailer is organized and maintains high standards for following the right procedures. Disorganization promotes inventory loss. If a retailer has low or inconsistent standards for inventory and organization in their stores, then they’re bound to find shortage, whether it’s from theft or administrative error.
One example of administrative error loss that always stood out to me is an investigation I worked on with a retailer who had losses in their fashion jewelry department. Because this type of merchandise is small and very easy to shoplift, we started looking at the loss from a theft perspective. After investigating the losses for a while, we eventually discovered that it wasn’t a case of shoplifting at all. Instead, employees did not want to take the time to display the merchandise properly, so they just threw it away. While this wasn’t truly a case of theft, there was definitely an issue with employee integrity that led to preventable administrative errors that needed to be resolved with improved employee training.
How to Identify Administrative Errors
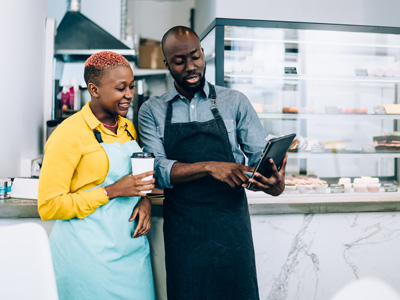
When you’re investigating any type of loss, you should always start with the assumption that it’s caused by theft. Think of it as working your way from the outside in. If you look for shoplifting and find nothing, and then investigate potential employee theft and still find nothing, then you can confidently focus your efforts on looking for administrative error in your organization.
Unfortunately, the challenge of investigating administrative error is that you often cannot identify these issues until you get the results of your inventory process. Back to the example with the black and red shirts: If you notice that you have only 75 black shirts when you ordered 100, you might not realize the source of the shortage until you do inventory and find an overage of 25 red shirts from the same vendor and a wash in overall shirts.
However, this isn’t exactly a negative either. Using the results of your inventory loss to look for instances of administrative error can help you develop solutions that are specifically tailored to your organization, which can help you prevent these losses from happening again.
One of the tell-tale signs of retail loss in general is low employee engagement. If your employees don’t care about the company, the store environment or their coworkers, then it’s likely they won’t care about following the proper procedures for inventory, receiving, stocking and more. Imagine this: If an employee doesn’t want to be at work, do you think they are going to follow the proper documentation protocol for damages?
Another effective way to identify administrative error in your organization is to conduct store visits in order to identify high-shortage departments. From there, you can investigate these losses to determine what kind of shrink you’re dealing with, whether it’s shoplifting, internal theft or administrative error.
A common sign of administrative error I found during my investigations was a full damage bin that hadn’t been processed in a long time. If a retailer allows their damages to build up, this could result in a higher chance of human error, simply because of the sheer quantity of damaged merchandise an employee must process. Employees might also believe that it’s acceptable for them to take damaged merchandise before it’s processed because it will be thrown away eventually — causing further discrepancies in your reconciliation process.
Another indicator of potential administrative error is item tags on the stockroom floor. If tags aren’t on your merchandise, whether they accidentally came off or were removed, there’s a chance an employee might put the wrong tag on an item. If an item is marked with the wrong price and stock keeping unit (SKU) number, it can cause an administrative shortage and eventually a true loss, if your products are sold at a lower price than they should be.
How to Prevent Administrative Error Loss
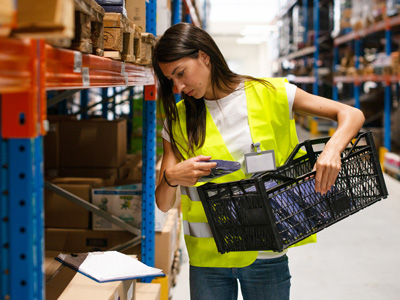
The good news is that loss caused by administrative error is 100 percent preventable. An awareness of both your products and your store environment is critical to preventing shortage. This isn’t just about preventing theft but organizing your stores to reduce the potential for mistakes.
One essential way to prevent administrative error loss is to prepare for inventory checks. I recommend that you create a planogram or a diagram of all the areas in your store with merchandise, including shelves, displays and your stock room. After drawing up the planogram, create a strategy to count every product in each area of your store in order to have a complete view of your inventory.
When planning your inventory check, make sure you’re not leaving out any areas of your store, especially displays and mannequins. I can’t count how many times I’ve worked with a retailer who had products on display that didn’t have tags and hadn’t been recorded into the inventory system. If you have merchandise on display that hasn’t been counted, this is still an avoidable loss that can be quickly recovered through proper reconciliation.
One of the biggest administrative error cases I worked on could have been completely avoided if there had been better communication between different departments within the organization. In this instance, the retailer had a 2-for-1 sale in their intimates department. However, the store employees weren’t trained on how to process the sale at checkout. Instead of ringing up each item, which would have accurately updated the store inventory, the cashier would just ring up one item and give the other item to the customer.
This led to a double loss according to the newly-inaccurate inventory data. Not only had the retailer not trained their employees on how to properly ring up these items, but they also hadn’t created a code for the 2-for-1 sale to be used with their point-of-sale (POS) system. Even if the employees knew that they should ring up each item, there was no protocol for them to apply the promotional discount to the purchase.
After realizing that the disorganized 2-for-1 sale caused them a major shortage that year, the retailer implemented new processes to address this mistake. With a more organized system, the marketing department collaborated with IT and store management to ensure that future sales had the necessary protocols to prevent any future administrative error. By taking the time to understand the processes behind a sales promotion, the retailer was able to save $300,000 in reduced losses.
Once you have a better idea of how administrative error happens in your company, you’ll become much better at spotting it in the future. This way, you can start looking for administrative error loss as part of your regular store operations, rather than just waiting for the results of your inventory checks. The most effective strategy for preventing administrative error loss is to pay close attention to the details and to collaborate at all levels within your organization to ensure clear communication and consistency when following protocols.
* * *
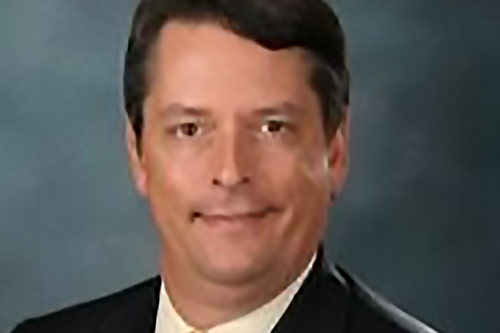
David Cutherell, CFI is senior vice president of business process automation at Prosegur USA. He spent 28 years in retail loss prevention, starting as a store detective and working his way up to senior leadership positions at Macy’s and Burdines. At Prosegur, David leads IT and business automation teams, with a special focus on business intelligence and data security.
Stay updated with the latest security trends and analyses by following Prosegur's blog.
-
How Data Analysts Drive Innovation in Hybrid Security
August 14, 2025
-
What Is a Site Security Assessment
August 6, 2025
-
Special Report: Los Angeles Protests Against ICE
June 11, 2025